Floating PV learning from aquaculture industry
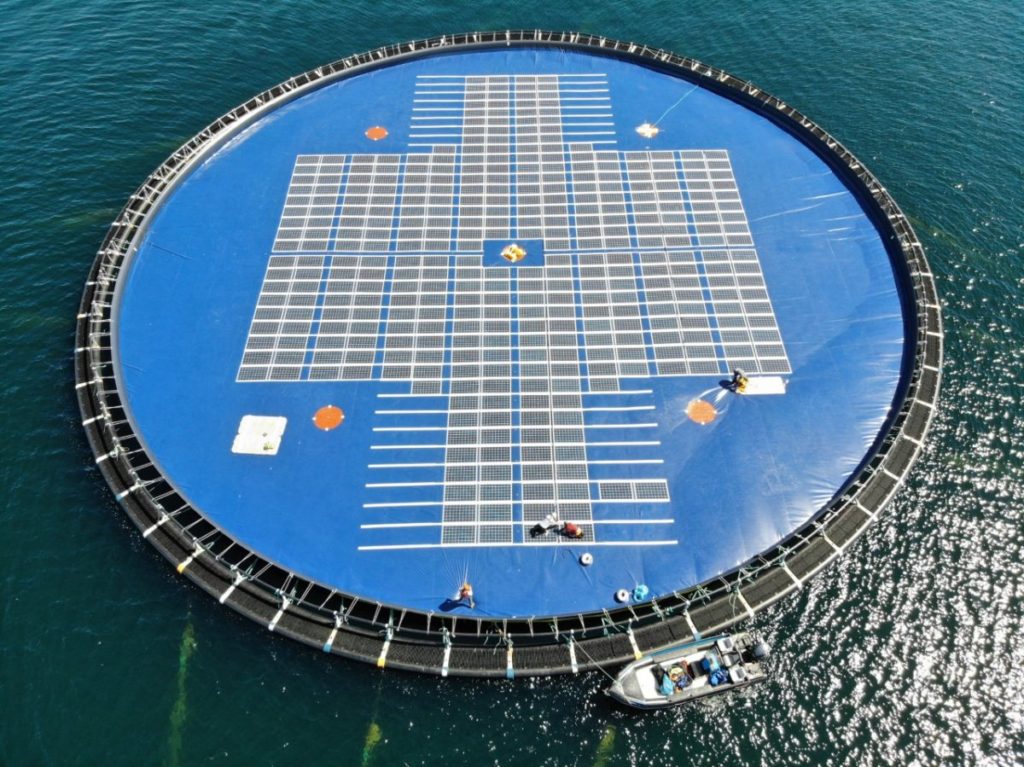
The CEO of Norwegian floating solar company Ocean Sun has spoken to pv magazine about his company’s innovative design for floating PV projects in near-shore locations and semi-sheltered waters. A pilot project built in the Philippines last year, said Børge Bjørneklett, is providing better-than-expected power output.
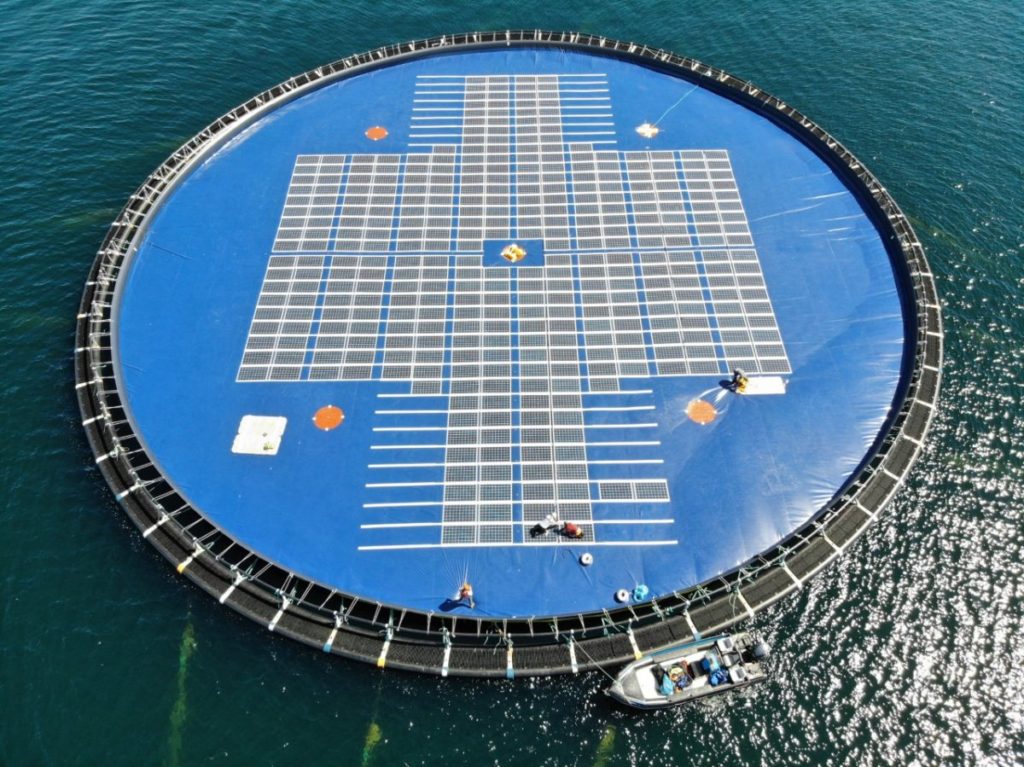
Norwegian quality assurance and risk management company DNV GL has awarded compatriot solar company Ocean Sun’s floating solar system design a conformity statement.
The paperwork verifies “the design methodology of the Ocean Sun floating solar structure, including design principles, methods and safety factors, complies with the relevant standards and recommended practices, such as the NS 9415 standard for Norwegian aquaculture”, DNV GL stated.
The NS 9415 marine fish farm standard establishes requirements for site survey, risk analysis, design and installation dimensions as well as for the production, installation and operation of fish farms. “This standard is very important for the Norwegian aquaculture industry,” Ocean Sun CEO Børge Bjørneklett told pv magazine. “It provides for very stringent rules for aquafarming facilities in order to avoid ecological disasters.”
Maritime expertise
Bjørneklett said damage to ocean-sited fish farms could result in farmed fish escaping and breeding with wild species. As a result, the Norwegian aquaculture industry has to comply with stringent standards relating to fish farm stability and robustness, especially with regard to structural design and mooring systems.
“Ocean Sun developed its special design for floating PV systems from this maritime expertise” said the CEO. “The design we developed, which is ideal for near-shore and semi-sheltered waters, is not exactly identical to that of a fish farm. I would rather say it is a derivative.”
The patented system consists of a floating buoyancy ring anchored to the seabed with four mooring points and twelve lines. “The difference with a fish farm is that there are no cages for the fish under the ring while most of the system weight is located on the surface where the modules are deployed,” Bjørneklett said.

“Structural design in the aquaculture industry has developed over several decades and the sector has learned several tough lessons from poor designs during the early years,” the CEO added. “For example, rectangular structures based on galvanized steel [have been] almost abandoned due to problems with corrosion and material fatigue at interconnections.”
Bjørneklett told pv magazine the circular shape and hydro-elastic behavior of the buoyant high-density polyethylene (HDPE) ring reduces problems which could otherwise occur if unfavorable winds and repeated waves hit the broadside of rectangular structures. The disk shaped floating membrane Ocean Sun uses in the center of its systems is also said to enhance integrity, similar to spokes in a wheel. The fully recyclable HDPE piping is readily available worldwide, making distribution easy, Bjørneklett added.
Membrane
The PV system’s floating ring features a membrane to which modules are attached. “The membrane is only 1mm thick and this is its special feature, as it allows … panels to be in direct thermal contact with the water, which contributes significantly to heat dissipation and, as a result, the modules’ yield is improved,” said the CEO.

The Ocean Sun boss did not provide details on the chemical composition of the material used, which he defined as an engineered polymer. He said a membrane could host around 600 kW of PV module generation capacity, with the size limit depending on the fact a single membrane occupies an entire 40ft container and larger membranes cannot be shipped overseas yet. “When we develop megawatt-sized projects, they are divided into 600 kW sub-units, with each unit being represented by a single buoyancy ring,” Bjørneklett said.
Modules and inverters
Ocean Sun used special modules provided by Chinese manufacturer GCL and string inverters from Chinese company Huawei in a 220 kw pilot project commissioned in the Philippines last year. “But our system is compatible with every kind of devices for both technologies,” Bjørneklett said.
The glass-glass modules used in that installation were conventional panels modified for the project. “The special waterproof junction boxes are located in the panel’s sunny side and the modules are connected to the membrane through marine-grade aluminum profiles which engage in welded attachment features in the membrane,” said the Ocean Sun CEO.
Inverters are usually located along the buoyancy ring and, if the floating system is very near the coast, can be installed on the shore.
Wind resistence
Bjørneklett said his company’s patented system also offers strong wind resistance. “Our system in the Philippines has been hit by tropical storms and so far no damage [was] detected,” he said. “As modules are completely flat on the membrane, wind drag is very low.” That claim, said the CEO, has been verified by computational fluid dynamics.
The Ocean Sun boss said the system also offers logistics advantages. “It can be deployed very easily and in a short time frame,” he said. “The ratio between its costs and performance are the best available in the floating PV market. Our pilot project in the Philippines is performing above all our expectations.”
Bjørneklett said the DNV GL is comparing the system’s performance with those of conventional floating PV and ground-mounted solar systems in Singapore. “The results are still not available but I am sure these will demonstrate our low-cost technology is highly performant,” the Ocean Sun chief added.
From: https://www.pv-magazine.com/2020/03/23/floating-pv-learning-from-aquaculture-industry/